球阀在一些特殊的场合下需要长期经受各类酸、碱、盐、氯离子、硫化物等强腐蚀性介质的侵蚀,在启闭过程中频繁经受摩擦、挤压等作用,因此球阀需要具有较好的耐腐蚀性能和耐磨性能。目前大多采用超音速火焰喷涂、等离子弧堆焊、氧乙炔喷焊和硬化合金等方法,将高硬度合金粉末掺杂WC等堆焊在密封面,虽然超音速喷涂的结合强度较高,但也存在生产成本高、变形量较大等缺点;等离子弧堆焊、硬化合金的方法又存在熔覆层疏松、缺陷多、基体热影响区大、生产周期长等缺点;氧乙炔喷焊虽然价格较低,但喷熔覆层与基体结合强度较低,不能承受交变载荷和冲击载荷。
激光熔覆技术可在钢材表面获得高性能的耐蚀、耐磨熔覆层,且熔覆层均匀致密、缺陷少、成品率高。与各种传统的堆焊、热喷涂、喷焊等只是机械连接相比,激光熔覆层与基体为冶金结合,质量和使用性能更优异。Co基自熔性合金粉末具有良好的高温性能和耐腐蚀、耐磨损性能,常被应用于石化、电力、冶金等工业领域的耐磨耐蚀耐高温等场合。然而,激光熔覆的工艺参数对熔覆层的性能起到极为关键的作用,因此,本文研究了激光功率对316不锈钢熔覆Co基合金粉末稀释率、组织与耐腐蚀性能,仅供阀门激光熔覆企业参考。
1 实验材料与方法
实验所用基体材料为球阀常用材料之一的316不锈钢,试样尺寸80mm×20mm×10mm。熔覆材料是Co基合金粉末,粉末粒径75~150μm,其实测成分见表1。
表1 Co基合金粉末成分(质量分数,%)

实验所用设备为HJ-4型串联5kWCO2激光器、三轴联动激光加工数控机床和同轴送粉系统组成,为防止熔覆过程中的氧化,用氩气进行保护。实验工艺参数为:光斑直径2.5mm,扫描速度800mm/min,搭接率40%,送粉量5g/min,激光输出功率分别为1.2、1.5、1.8、2.1和2.5kW。
激光熔覆后,沿熔覆层横截面制取试样,按金相制样标准进行研磨和抛光,用王水(HNO3∶HCl=1∶3)腐蚀。使用JSM-6300的场发射扫描电镜观察组织及扫描电镜自带能谱进行元素分析;用SISCIASV8.0金相图像分析软件测量熔覆层高度以及基材的熔化深度,并计算其稀释率;采用阿美特克IM6E电化学综合测试仪检测熔覆层耐腐蚀性能。
2 结果与讨论
2.1 熔覆层的稀释率及能谱分析
稀释率是决定熔覆层质量的重要参数。激光熔覆层稀释率的变化不仅会改变熔覆层材料内部的化学成分,使其原有的性能(如高硬度、耐磨性能和抗氧化性能等)发生改变,而且将直接影响到熔覆层与基体间的结合强度。
本实验将激光熔覆后的试样沿垂直于熔覆方向切开,用扫描电镜拍取照片,熔覆层的高度H、基材的熔化深度h的测试方法如图1所示。
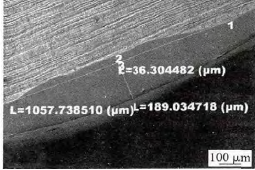
图1 稀释率测量方法
实验中稀释率η的计算公式由面积法简化为:
η=(h/h+H)×100% (1)
不同功率测量结果及由公式(1)所计算的稀释率如表2所示。
表2 不同功率熔覆层的尺寸及稀释率
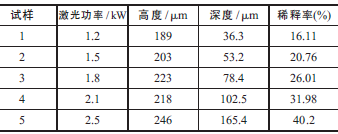
由表2可以看出,激光功率为1.2kW时,熔覆层的稀释率*低,为16.11%,随激光功率的增加,熔覆层的稀释率与激光功率成正比,当激光功率为2.5kW时,稀释率*大(40.2%),这是因为,随激光功率的增加,在其它工艺参数一定的情况下,激光功率越大,基材熔化的越多,在熔池搅动的过程中混入熔覆层而引起合金成分变化的程度就越大,即稀释率越大。过大的稀释率将导致损害熔覆层固有的性能,加大了熔覆层开裂、变形的倾向,也会对耐腐蚀性能产生影响,但是,没有一定量的稀释率也会影响熔覆层与基体的冶金结合。
图2是2.5kW功率熔覆后试样的SEM组织及能谱分析。可以看出,试样在王水的腐蚀下,基体316不锈钢腐蚀严重,而熔覆层组织的晶界刚开始显示,晶粒细小均匀,因此从图2可以看出,熔覆层的耐腐蚀性能要明显优于基材316不锈钢。此外,对熔覆层进行区域扫描,区域位置及扫描结果如图2所示。分析结果显示,熔覆层中存在C、Si、Cr、Fe、Co、Ni等元素,激光熔覆前,粉末中Co基合金粉末的Co含量约60%,而图2中显示的Co元素的质量分数仅为5.94%,同时,Fe元素的含量由之前的1.85%增加到61.26%,说明在激光熔覆过程中,熔化的粉末与不锈钢基体材料发生了较多的对流和扩散。
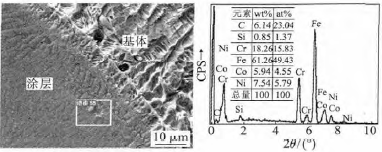
图2 熔覆层组织及能谱分析(激光功率2.5kW)
2.2 熔覆层耐腐蚀性能
利用电化学综合测试仪对不同的激光功率在3.5wt%NaCl溶液中的腐蚀行为进行测试,对5组不同激光功率下的熔覆层的耐腐蚀性能进行比较,其实验结果如表3、图3所示。对图3中阳极极化曲线进行塔菲尔(Tafel)拟合,其数据结果如表3所列。
表3 不同激光功率熔覆层的耐腐蚀性能参数
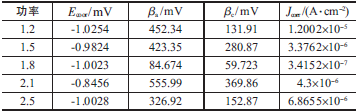
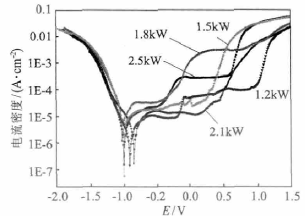
图3 不同激光功率的融覆层的电极化曲线
通过图3和表3可以看出,激光功率为1.2~1.8kW时,材料的自腐蚀电位均在-1.0左右,相差不大,而电流密度随激光功率的增加呈数量级降低,从1.2002×10-5A•cm-2降低至5组激光功率中的*低值3.4152×10-7A•cm-2,这表明在激光功率为1.8kW时,其耐腐蚀性能相对*佳;当激光功率为2.1kW时,虽然电流密度又升至6.8655×10-6A•cm-2,但其自腐蚀电位降了0.15mV左右,可以得出激光功率为2.1kW时也具备较好耐腐蚀性能;而当激光功率为2.5kW时,自腐蚀电位又开始降低,电流密度开始增加,即耐腐蚀性能又开始下降。因此,当激光功率为1.8~2.1kW时,熔覆层的耐腐蚀性能较好。
结合电化学腐蚀原理及晶粒细化对耐腐蚀性能的影响,随激光功率变化,熔覆层耐腐蚀性能变化的原因可解释为:随激光功率的增大,激光束的能量越来越大,激光束的加热温度越来越高,而不同激光功率下的冷却的介质相同,所以导致随激光功率越来越大过冷度越来越大,这样熔覆层中的合金元素能够很快地形成数量非常多的非自发晶核,从而使形核率大大提高,形成的显微组织也越来越细小。显微组织的细小使得单位晶界上的杂质的含量值变得很低,并且在快速冷却过程中的成分偏析减少,成分偏析的减少降低了由于形成原电池而导致的电化学腐蚀。另一方面,当晶粒细化时,使材料活性原子数目增加,促使材料表面钝化膜的生成能力增加(初期的自腐蚀电流密度较大),使其表面更易形成钝化膜,从而提高了材料的钝化性能。然而,由前面的分析可知,当激光功率增加到一定程度后,稀释率也随之增加,导致熔覆层与基体的元素交流变大,使得熔覆层起到耐腐蚀作用的Co、Cr等元素相对降低,从而导致耐腐蚀性能下降。
3 结论
(1)随激光功率的增大,熔覆层的稀释率逐渐增大,由1.2kW时的16.11%增加至2.5kW时的40.2%,此时熔覆层与基体的合金元素有较大的对流与扩散,这也是熔覆层耐腐蚀性能变化的原因之一。
(2)随激光功率的增大,熔覆层的耐腐性能先提高后降低,激光功率为1.8~2.1kW时具有较好的耐腐蚀性能,当激光功率为2.1kW时,熔覆层的自腐蚀电位*低,为-0.8456mV,当激光功率为1.8kW时,熔覆层的腐蚀电流密度为*小的3.4152×10-7A•cm-2。
(3)耐腐性能变化是因为有晶粒细化提高耐腐蚀性能及稀释率增加降低耐腐蚀性能,随激光功率增加,前期晶粒细化带来的耐腐蚀性能增加要大于稀释率增加所导致的耐腐蚀性能降低,而后期则刚好相反。